
Anyone who knows me personally know that I’m a big Adventure Time fan. I love the nonsensical nature of the show as it provides a nice relaxing escape. Lately I’ve been gathering all the pieces for my Trek Madone 5.2. It’s not really a 5.2 as it is not going to be kitted out with Shimano (Ultegra) gear. It will receive my SRAM Rival group set that was purchased a few years ago and put on my GT GTR Series 4 which had originally came with Sora / ST-2200 shifters. I’ve tried to keep my bike with my ability level – however a Madone 5 Series is well beyond my need. I promise this is going somewhere. Just stick with me after the break.
Commentary
While I’ve trained with what I’ll call “Virtual Power”, which is using the regression curves for my Kurt Kinetic for 3 winters now, I haven’t experienced outdoor power until now. It is a very different experience having those numbers in front of you on a road. It’s teaching me it’s hard to zone in on a specific number and stay there. For my weight (100kg, I’m a big, dense boy) I’ve found that if I don’t push 400-500 watts then I don’t really go up even the smallest of hills very quickly. I recently read in the Wattage group that you really need a year of playing before you can seriously use this data. I’d say I’m not a novice, but I am not intermediate with data.
Having used this “Virtual Power” for a few years I thought I would be decent at evaluating power meters and what makes them good or bad. I’m a much more technical person, and as such I consistently forget that the coaches and athletes who use these tools while not knowing really how they work really. They don’t understand what would make one better than the other, which is why most people blindly say one is better than the other without understanding the technical merits of one over the other.
I’m not making any evaluations on products here, but I’ve been reading quietly in a lot of forums. In a previous post I showed how strain gauges, even in thermally compensated designs, can drift – very repeatedly drift as a function of temperature. A “good” auto-zero algorithm would adjust the zero based on this temperature – the holy grail, the platinum standard, etc, of power meters which wouldn’t require the user to do so much interacting. I don’t know the algorithms used by Powertap, SRM, Quarq, Rotor Power, etc but I do know that I am incorporating an auto zero adjustment because it will make it more accurate.
Rounding full circle to how I began, I will soon have a bike of very high level equipped with a tool that I think should be bought long before other bike upgrades but most people won’t get a power meter until they have a 4000 dollar bike. I am in no way capable of fully utilizing the performance of such a high quality frame. I’m nervous about this frame but not for the reasons you would expect. I’m nervous because showing off my prototype on it may illicit feelings that this is going to be another 2000 dollar plus product.
My goal in trying to create a lower cost power meter is to allow those aluminum framed, entry level, Shimano 105 / SRAM Apex/Rival / Campy Athena people who want to train more effectively to do so. It’s the 1500 – 2500 dollar bike people. The people who’s bike is equivalent to the price of one of these training tools currently. I think I will keep my 2008 GT GTR frame such that when I show off the new prototypes I can show them working on both my old used aluminum frame and my new carbon bike.
Progress Update
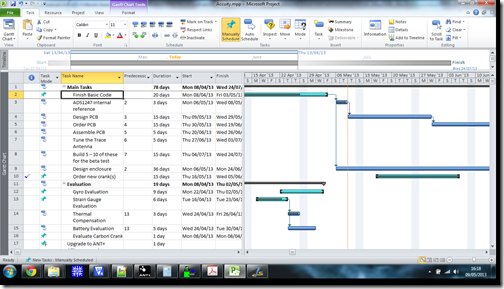
Seriously, I want to give a huge shout out to the people who made Arduino possible. What they did was translate the cryptic language of microcontrollers to something more easily digestible and along the way made some simple tools. I’ve been stuck for two plus weeks on “Basic Code”. I’ve been stressed out because it’s been improbably annoying to replicate the millis() function of the Arduino which is necessary for calculating cadence from any pulse type sensor. It had to do with existing “Timer.c” library that came in the reference code. It was quite annoying.
This has throw off the schedule somewhat, however I believe I have it sorted finally. However, in sorting this out I found out that the reference code doesn’t work like I thought it did and is therefore less power efficient than I thought. This comes as a surprise, though I am seriously behind on a couple of tasks. The Gyro Evaluation still shows up and I still want to do it, but it’s hard to make it happen. The priority now is the current measurements. I have to get this done this weekend now that the cadence calculation is almost worked out. At least I’m 3 weeks ahead on ordering cranks.
I really wanted to be doing PCB design this week which is why I took three days off work – such that I could do more work. Who knows, I might get to start on it yet.