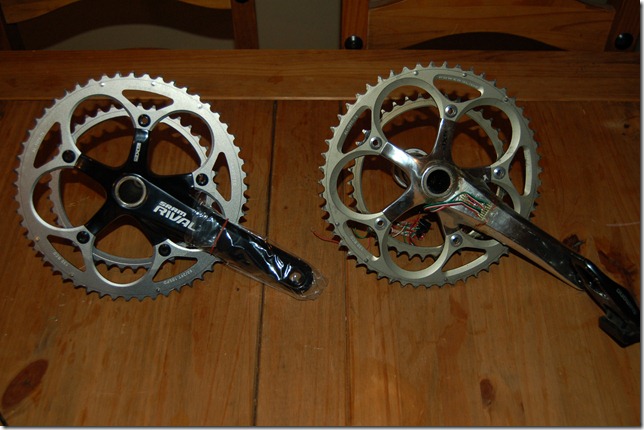
Earlier this week my new crank arrived ready to instrument. The above picture is the new crank with V2 Power Meter (currently disassembled). The new OCT hollow cranks have a flat back instead of the grooved out backing of the old pre-OCT model. This is exactly what I was expecting for two reasons.
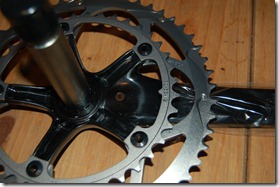
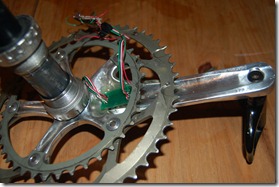
The first reason being is that the flat back is easy to mount to. Secondly, and more importantly, if a shear gauge is used to measure the drive side arm it can be placed on the inside and is thus protected. Another view is of the non-drive side arm shown below. In V3 the non-drive side arm will not be instrumented. The torque tube that goes through the bottom bracket is instrumented instead. No wires to be run through the crank, or like Vector or Rotor, both sides do no require batteries, a master and a slave connection and the associated issues.
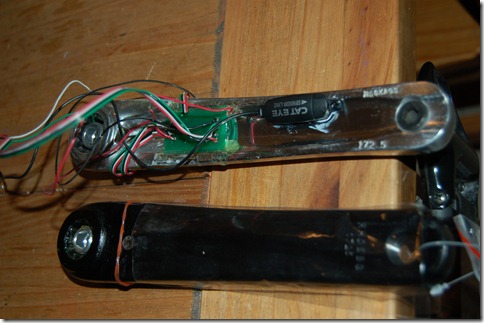
The first thing is to remove the chain rings as they get in the way. I didn’t do this on the previous builds. The loctite on the chain rings tend to make them very difficult to start backing off. I was getting some very large flex in my Allen keys. Two socket drivers work best, or a socket driver on the small side and an Allen key on the other.
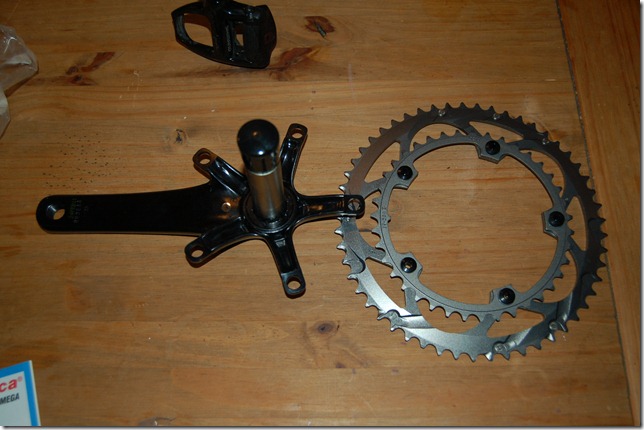
On that singular polymide backing is 4 strain grids. There has been some confusion caused by power meter manufacturers. A gauge is the grid(s) on a polymide backing. In this cause this is one strain gauge that has four sensing grids. However for marketing purposes this would be referred to as four strain gauges. I could use single grid gauges but that is an inherently flawed design that is more time consuming. It’s primary flaw is that each grid could be aligned poorly, there is a greater propensity for a bad glueline, harder to mask the areas, etc.
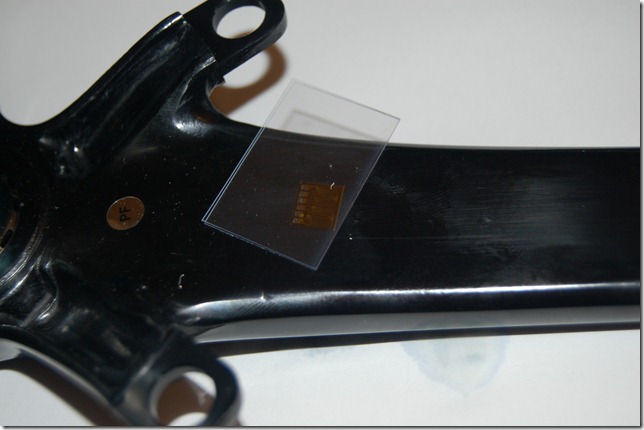
I used masking tape to mask off the area but when using Vishay Conditioner and sanding with 180, then 320, then 600 grit paper destroyed it very quickly. I masked the area with PCT-2M tape instead and continued sanding. This or their MGJ mylar tape works best for masking.
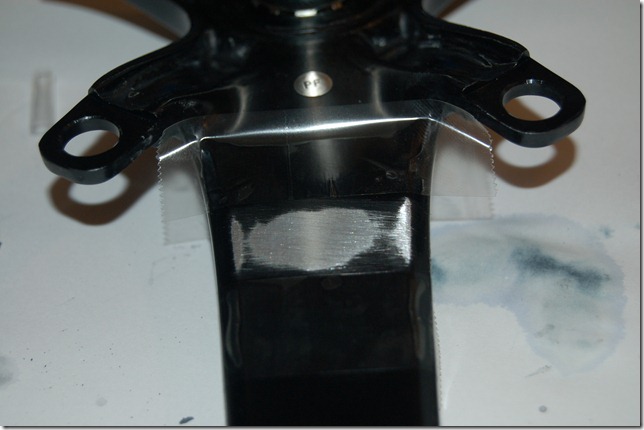
After sanding with conditioner, flood the area, wipe with gauze, then flood with neutralizer and scrub with cotton applicators (Q-tip with wooden stick) until no more metal residue comes up. Flood with neutralizer again and then wipe away with clean gauze – do not reuse, wipe in one direction only, and don’t wipe with anything that contacted your sink. Those oils can ruin the glueline.
After cleaning a piece of glass or plastic with neutralizer, place the gauge down and use the PCT-2M tape as shown to pick it up. Remove the tape and gauge with by peeling back at a shallow angle.
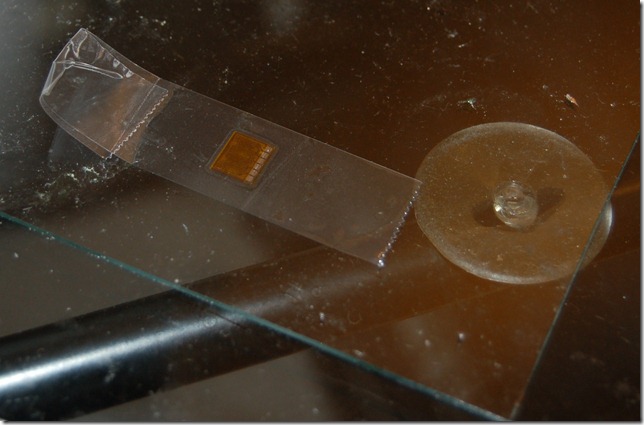
Apply to the prescribed area. Peel the tape back, again, at a shallow angle, apply accelerator, wait for it to dry, then apply glue to the surface just before the gauge and wipe the gauge down with gauze from back to front, then apply finger pressure. The APP Note from Vishay best describes this and it requires some practice to get right.
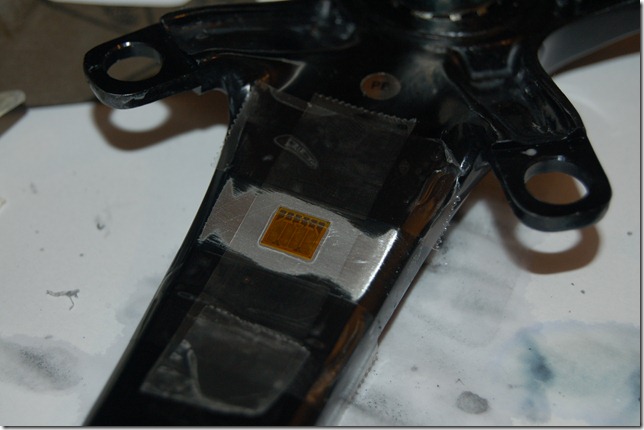
While waiting for this to dry onto the hard part. The gauge in the hole. The gauge needs to be laid on a clean metal surface because the wires will need to be soldered to it. Cover the gauge except the contacts with PCT-2M tape.
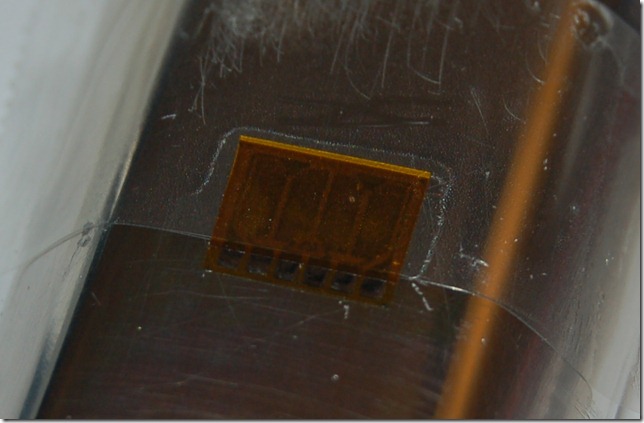
Now, painstakingly apply flux, tin the contacts, tin the fine magnet wire, and solder on the wires. It’ll start looking like the picture below after using solvent to remove the tape ever so carefully.
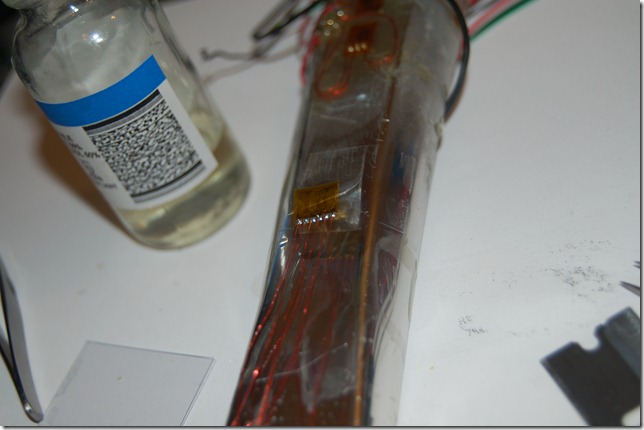
Place the gauge in a clean bottle of solvent to remove any flux or residue.
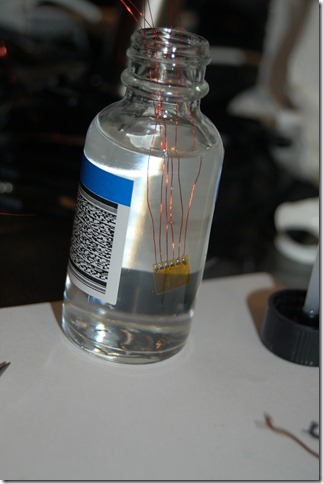
The next steps were impossible to really photograph, but I did manage to get me applying pressure to the gauge while it’s in the hole.
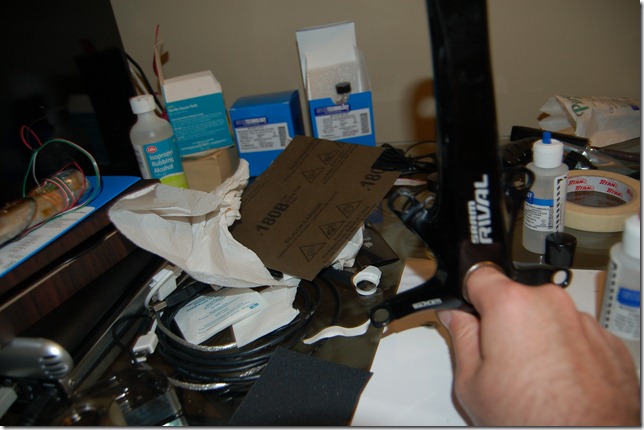
It’s hard to see but the gauge is in there.

Using the M-Coat A, the inside gauge is coated and let to set.
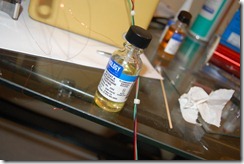
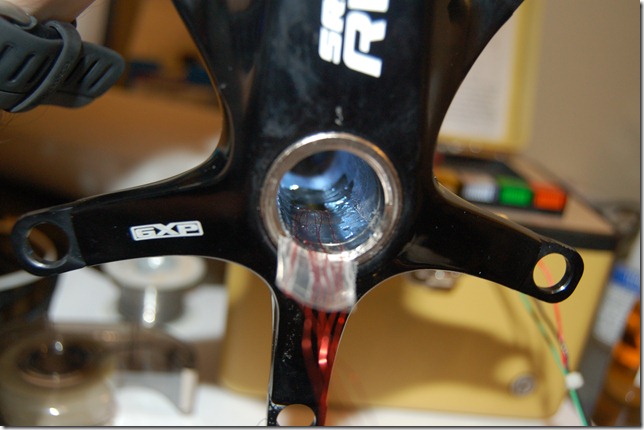
Below is how the soldering looks on the arm. This is then flooded with solvent, let dry, and then coated with M-Coat A. The gauges have their resistance checked by a Vishay Gauge Installation tester 1300. These pricey little old school looking boxes are high quality resistance measurement units. They can also measure in the Gohm range for resistance to ground and do this with 10VDC which is safe for almost all gauges.
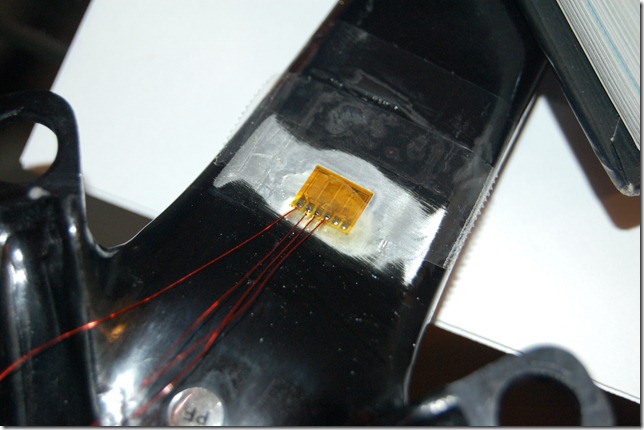
More updates coming soon. I have a National Instruments Compact DAQ this weekend that I will be testing the installation sensitivity with.